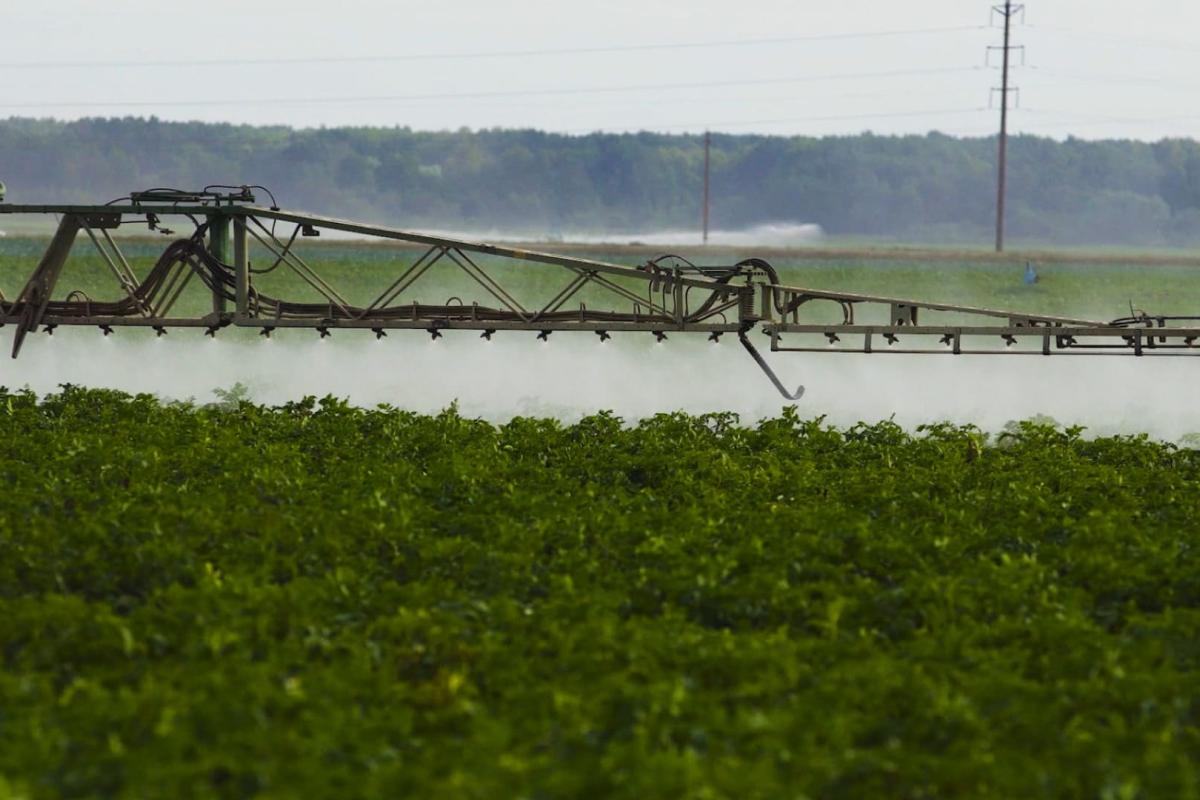
Overview
This service helps you understand where your AI-powered product, system, or software stands in terms of technological maturity. We conduct a basic, yet structured evaluation of your solution—including physical testing of selected components and general system behaviour—to identify its current development stage and key areas that need improvement. We also assess the quality of documentation, system architecture, and software implementation. For example, when evaluating an apple-picking robot, we assess the readiness and integration of its core subsystems: the gripper mechanism, robotic arm kinematics and control, and the vision system responsible for detecting ripe fruit. We analyse areas where current solutions can be improved or require some redesign and whether the robot as a whole can effectively perform “scene ”cleaning”—removing ripe apples while preserving unripe ones and the plant structure. Based on our findings, we prepare a clear roadmap and a development plan with recommendations for the next steps, which may include further testing or refinement through other agrifoodTEF services. As part of the process, we also confirm the current Technology Readiness Level (TRL) of each major component. The outcome helps you focus your R&D work and understand what is still required to move your solution closer to full deployment and commercial readiness.
More about the service
physical testing of hardware components (e.g., gripper and robot arm) combined with remote analysis of software, system logic, and sensor integration.
Multiple expert teams may assess the robot’s individual subsystems in parallel. We begin with building or sourcing a basic test environment to evaluate repeatable performance.
This setup allows us to test individual modules (e.g., in the case of apple-picking robot gripper endurance, fruit removal dynamics) as well as system-level behaviours (e.g., picking trajectory, stability of the base during operation).
The process may include, i.e.,- Physical tests of the gripper: how many picking attempts the plant can withstand, risk of damaging the plant, and effectiveness of removal.
- Kinematic tests: robot arm movement toward and away from fruit, based on coordinates (e.g., stem and basket location), including hand-inputted berry positions.
- Vision assessment: Is the system capable of identifying ripe fruit and avoiding unripe ones?
- Evaluation of integration: how the robot behaves as a whole, especially in terms of reach, balance, and stability during the harvesting process.
Customers must provide a functional prototype and access to the source code (if applicable), along with technical documentation. Based on these inputs, we deliver a detailed report outlining the current state, strengths and weaknesses, and clear next steps—including matching the needs to relevant agrifoodTEF services for further development.
The scope and methodology are defined based on the available inputs and the technological maturity of the product. To carry out the assessment, the customer must provide access to a working prototype (in the case of hardware), full technical documentation, and, where applicable, access to the source code.
The evaluation may include simplified tests of selected components or system behaviour, especially when integration or subsystem functionality is in question. The service outcome—including the report format, level of detail, and scope of recommendations—can be customised based on the client’s expectations and needs. Follow-up consultations or workshops can also be arranged to support the implementation of proposed next steps or further development via other agrifoodTEF services.